Izolacja armatury
Izolacja armatury odgrywa kluczową rolę w minimalizacji strat ciepła i zwiększeniu trwałości instalacji. Sprawdź, jak nowoczesne rozwiązania mogą pomóc w oszczędzaniu energii i zapewnieniu bezpieczeństwa systemów przemysłowych.
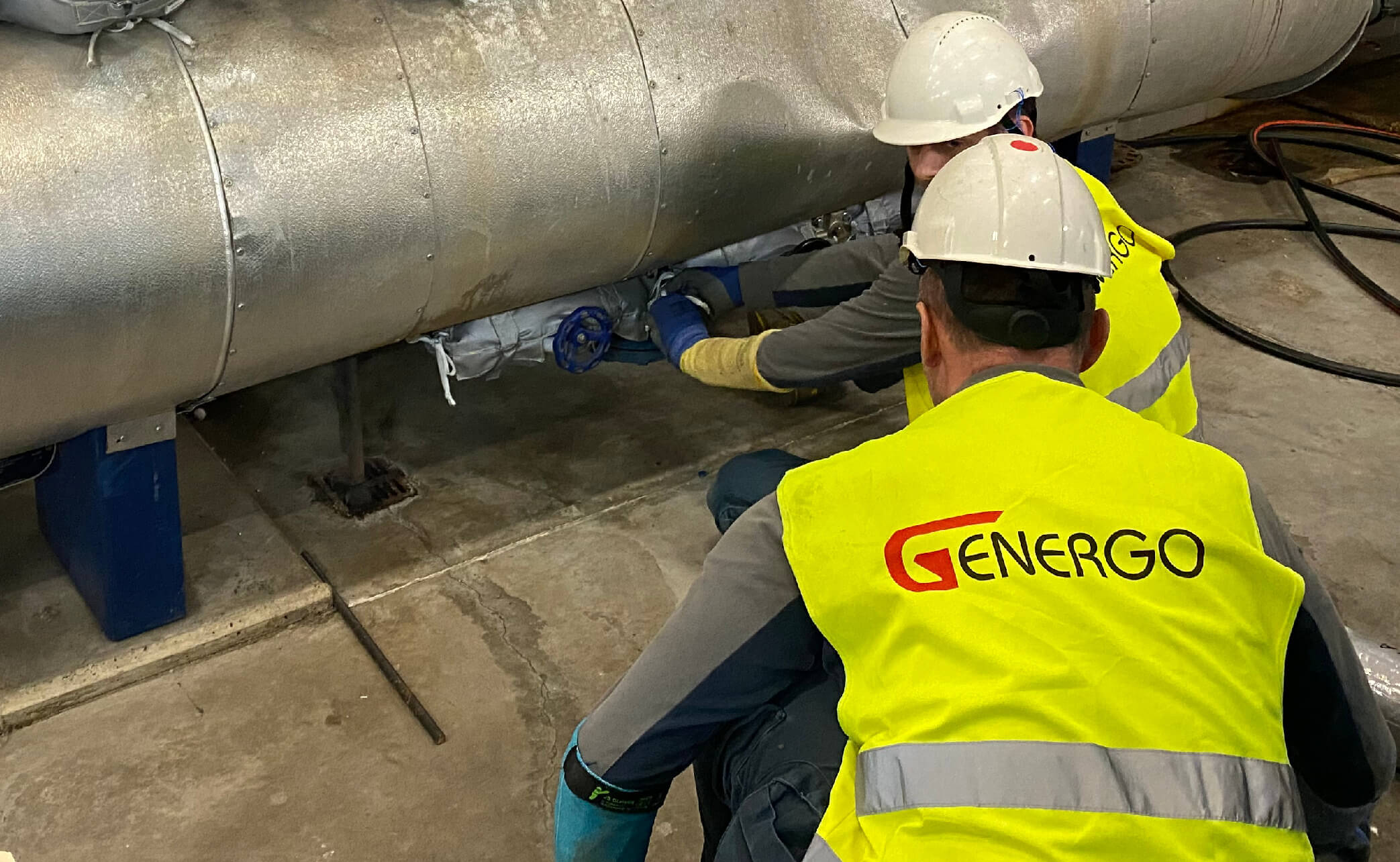
Izolacja termiczna armatury odgrywa kluczową rolę w systemach grzewczych i ciepłowniczych, wpływając bezpośrednio na efektywność energetyczną i redukcję strat ciepła. Właściwie zaprojektowana i wykonana izolacja przemysłowa pomaga zminimalizować straty energii podczas transportu ciepła przez instalacje, urządzenia i armaturę, co przekłada się na niższe koszty eksploatacji oraz ochronę środowiska poprzez zmniejszenie emisji CO₂.
Straty ciepła, które występują w niezabezpieczonych termicznie elementach instalacji, mogą prowadzić do znacznych strat energetycznych, a w konsekwencji do zwiększenia kosztów operacyjnych.
Armatura przemysłowa co to jest?
Armatura przemysłowa to zbiór urządzeń i elementów instalacyjnych stosowanych w różnego rodzaju systemach przemysłowych, takich jak instalacje wodociągowe, grzewcze, chłodnicze, gazowe czy ciepłownicze. Obejmuje ona m.in. zawory, przepustnice, zasuwy, kurki, filtry, odwadniacze i inne komponenty, które kontrolują przepływ, kierunek, ciśnienie lub temperaturę różnych mediów (np. wody, pary, gazów, chemikaliów) w instalacjach.
Armatura przemysłowa odgrywa kluczową rolę w zapewnieniu bezpiecznej i efektywnej pracy systemów przemysłowych.
Izolacja armatury
Ze względu na swoją konstrukcję i umiejscowienie w instalacji, armatura jest szczególnie narażona na straty ciepła. Izolacja armatury jest zatem niezbędna, aby zapewnić jej optymalne działanie i zapobiec niepożądanym stratom energii. Właściwa izolacja armatury nie tylko chroni ją przed utratą ciepła, ale także zabezpiecza przed kondensacją pary wodnej oraz korozją, co w efekcie zwiększa trwałość całej instalacji. Zastosowanie odpowiednich materiałów izolacyjnych oraz ich prawidłowy montaż są kluczowe dla efektywności energetycznej i niezawodności systemów grzewczych i ciepłowniczych.
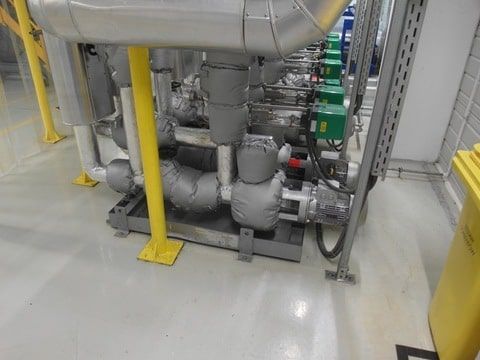
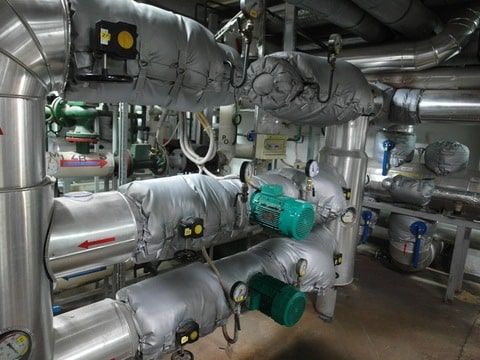
Izolacja armatury zastosowanie
Termoizolację stosuje się do elementów armatury takich jak:
- Zawór kulowy,
- Zawór odcinający,
- Zawór skośny z siłownikiem tłokowym,
- Zawór zwrotny,
- Filtr siatkowy,
- Separator parowy,
- Moduł odwadniający,
- Odwadniacz pływakowy,
- Odwadniacz dzwonowy,
- Zawór redukcyjny,
- Pompa kondensatu,
- Odwadniacz pompujący,
- Zawór bezpieczeństwa itp.
Rodzaje izolacji stosowanej na armaturze
Izolacja właściwa armatury przemysłowej
Izolacja właściwa to kluczowy element systemu izolacyjnego stosowanego na armaturze, którego głównym celem jest ograniczenie strat ciepła i zapewnienie efektywności energetycznej instalacji grzewczych oraz ciepłowniczych. Izolacja ta obejmuje warstwę lub warstwy materiałów o niskim współczynniku przewodzenia ciepła, które minimalizują przenikanie energii cieplnej do otoczenia.
Materiały używane do izolacji właściwej:
- Materiały włókniste: Wełna mineralna i szklana są powszechnie stosowane ze względu na swoją wysoką odporność na temperatury oraz doskonałe właściwości izolacyjne. Są one często stosowane w formie mat, płyt czy otulin.
- Porowate tworzywa sztuczne: Pianka poliuretanowa, która może być aplikowana jako natrysk, tworzy jednolitą warstwę izolacyjną, dobrze przylegającą do powierzchni armatury.
- Sztywne kształtki izolacyjne: Wykonywane z porowatych materiałów, takich jak styropian lub specjalistyczne tworzywa sztuczne, zapewniają precyzyjne dopasowanie do kształtu armatury, co zwiększa efektywność izolacji.
Pokrowce termoizolacyjne wykonane z nowoczesnych materiałów umożliwiają bezproblemowe odizolowanie fragmentu lub całości instalacji, np. przy okresowych przeglądach technicznych połączeń kołnierzowych, pomp, odwadniaczy i innych.
Wymagania dotyczące odporności izolacji właściwej:
- Odporność na wysokie temperatury: Materiały izolacyjne muszą być odporne na maksymalne temperatury eksploatacyjne, które mogą występować w systemie, aby zapobiec ich degradacji.
- Odporność na działanie wody: Izolacja armatury musi być zabezpieczona przed wnikaniem wody, która mogłaby obniżyć jej właściwości termiczne oraz prowadzić do korozji elementów instalacji.
- Odporność chemiczna: Materiały izolacyjne powinny być chemicznie obojętne względem substancji, z którymi mogą się stykać, aby uniknąć reakcji chemicznych, które mogłyby uszkodzić zarówno izolację, jak i samą armaturę.
Płaszcz ochronny izolacji armatury
Płaszcz ochronny to zewnętrzna warstwa izolacji armatury, która pełni funkcję ochronną, zabezpieczając izolację właściwą przed uszkodzeniami mechanicznymi oraz wpływem niekorzystnych warunków atmosferycznych. Płaszcz ten jest niezbędny do zapewnienia długotrwałej efektywności izolacji termicznej oraz ochrony instalacji przed czynnikami zewnętrznymi.
Funkcje płaszcza ochronnego izolacji armatury:
- Ochrona izolacji armatury przed uszkodzeniami mechanicznymi: Płaszcz zabezpiecza izolację właściwą przed przypadkowymi uderzeniami, ścieraniem i innymi uszkodzeniami, które mogą wystąpić podczas montażu lub eksploatacji instalacji.
- Zabezpieczenie izolacji armatury przed wpływem warunków atmosferycznych: W przypadku instalacji narażonych na działanie czynników atmosferycznych, takich jak deszcz, śnieg czy promieniowanie UV, płaszcz ochronny odgrywa kluczową rolę w zabezpieczeniu izolacji przed degradacją.
- Estetyka i łatwość konserwacji izloacji armatury: Płaszcz ochronny nadaje izolacji estetyczny wygląd oraz umożliwia łatwiejsze utrzymanie jej w czystości, co jest szczególnie ważne w instalacjach przemysłowych i budynkach użyteczności publicznej.
Materiały stosowane do wykonania płaszcza ochronnego izolacji armatury:
- Blacha stalowa ocynkowana: Jest powszechnie stosowana ze względu na swoją wytrzymałość oraz odporność na korozję. Idealnie nadaje się do ochrony izolacji w trudnych warunkach środowiskowych.
- Aluminium: Taśmy aluminiowe są lekkie, odporne na korozję i łatwe do formowania, co sprawia, że są często używane w mniej wymagających aplikacjach.
- Folie z tworzyw sztucznych: Stosowane tam, gdzie wymagane jest lekkie, elastyczne, ale trwałe rozwiązanie, które zapewni ochronę przed wodą i wilgocią.
- Włókno szklane pokryte warstwą teflonu: nowoczesne rozwiązanie stosowane w pokrowcach Genergo np. w THERMO-GEN CLEAN™ zapewniają doskonałą barierę dla wody, oleju, detergentu czy kwasu.
Stosowanie odpowiednich materiałów do izolacji właściwej oraz płaszczy ochronnych jest kluczowe dla zapewnienia długotrwałej ochrony termicznej armatury. Właściwa izolacja armatury nie tylko przyczynia się do zmniejszenia strat ciepła, ale także chroni instalację przed uszkodzeniami i przedłuża jej żywotność, co jest istotnym elementem w dążeniu do maksymalnej efektywności energetycznej systemów grzewczych i ciepłowniczych.
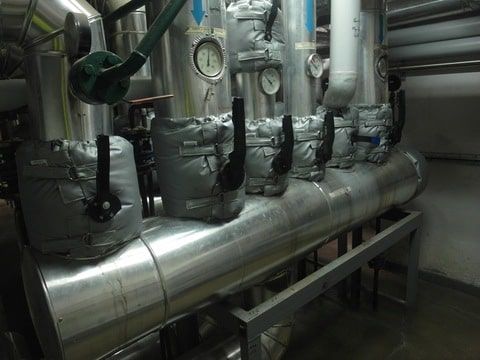
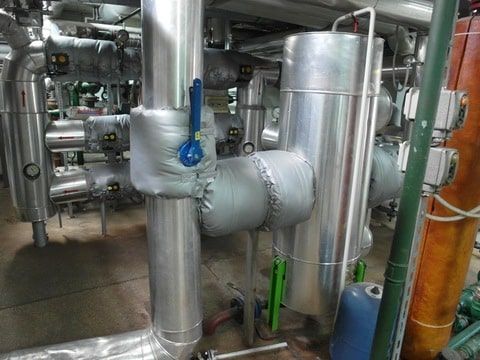
Zasady projektowania izolacji armatury
Dokumentacja techniczna izolacji termicznej armatury jest kluczowym elementem procesu projektowania instalacji grzewczych i ciepłowniczych. Powinna zawierać wszystkie niezbędne informacje umożliwiające prawidłowe zaprojektowanie, wykonanie i odbiór izolacji. Oto podstawowe elementy, które powinny znaleźć się w takiej dokumentacji:
- Specyfikacja materiałów: Dokładne określenie materiałów, które mają być użyte do izolacji właściwej oraz płaszcza ochronnego. Ważne jest, aby materiały te były dobrane zgodnie z wymaganiami dotyczącymi odporności na temperaturę, wodę oraz czynniki chemiczne.
- Grubość izolacji armatury: Określenie wymaganej grubości izolacji w zależności od rodzaju instalacji i temperatury przesyłanego medium. Grubość ta powinna być dobrana tak, aby zapewnić minimalne straty ciepła oraz spełniać wymogi normy PN-B-02421.
- Liczba warstw izolacji armatury: Informacje dotyczące liczby warstw izolacji oraz grubości handlowej (produkcyjnej) użytych materiałów, co jest istotne dla zapewnienia równomiernej i efektywnej izolacji.
- Rysunki konstrukcyjne: Szczegółowe rysunki pokazujące sposób mocowania izolacji oraz płaszcza ochronnego, w tym detale techniczne dotyczące montażu na armaturze.
- Zestawienie materiałów: Lista materiałów i akcesoriów potrzebnych do wykonania izolacji, co ułatwia zamówienie i przygotowanie odpowiednich komponentów na placu budowy.
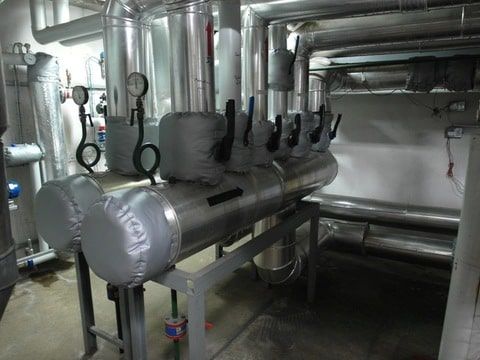
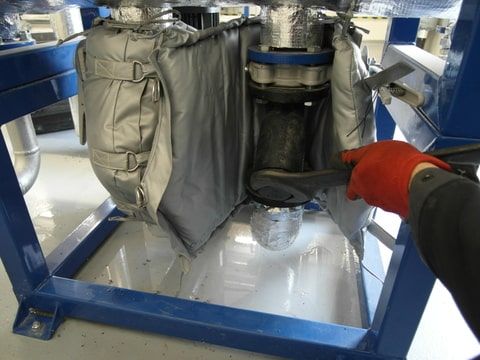
Dobór grubości izolacji armatury
Dobór odpowiedniej grubości izolacji jest jednym z najważniejszych aspektów projektowania izolacji armatury. Grubość izolacji powinna być dobrana w taki sposób, aby zapewnić optymalną ochronę przed stratami ciepła, przy jednoczesnym uwzględnieniu warunków eksploatacyjnych i ekonomicznych.
- Rodzaj instalacji: W zależności od tego, czy armatura znajduje się w instalacji centralnego ogrzewania, ciepłej wody użytkowej czy sieci ciepłowniczej, grubość izolacji będzie się różnić. Norma PN-B-02421 określa minimalne grubości izolacji dla różnych rodzajów instalacji, uwzględniając przy tym średnicę nominalną rurociągu oraz temperaturę przesyłanego czynnika.
- Temperatura czynnika grzewczego: Im wyższa temperatura czynnika grzewczego, tym większa powinna być grubość izolacji, aby skutecznie zapobiec stratom ciepła.
- Warunki eksploatacyjne: Dodatkowe czynniki, takie jak lokalizacja armatury (np. w pomieszczeniach ogrzewanych czy nieogrzewanych, w kanałach podziemnych lub na zewnątrz budynków), mogą wpływać na konieczność dostosowania grubości izolacji. W niektórych przypadkach, zwłaszcza tam, gdzie izolacja jest narażona na działanie wilgoci lub agresywnych substancji, może być konieczne zwiększenie grubości izolacji lub zastosowanie dodatkowych zabezpieczeń.
Wytyczne montażowe dla izolacji armatury
Prawidłowy montaż izolacji na armaturze jest kluczowy dla zapewnienia jej efektywności i trwałości. Oto kluczowe zasady, które należy uwzględnić podczas montażu:
- Przygotowanie powierzchni armatury: Przed nałożeniem izolacji, powierzchnia armatury powinna być dokładnie oczyszczona i sucha. Wszelkie zanieczyszczenia, oleje czy rdza muszą zostać usunięte, aby zapewnić odpowiednią przyczepność izolacji.
- Montaż kształtek izolacyjnych armatury: Kształtki izolacyjne powinny być tak dobrane, aby ściśle przylegały do powierzchni armatury. Styki pomiędzy poszczególnymi elementami izolacji muszą być dobrze dopasowane i przesunięte względem siebie w kolejnych warstwach, co zapobiega tworzeniu się mostków termicznych.
- Zastosowanie płaszcza ochronnego izolacji armatury: W zależności od warunków eksploatacyjnych, na izolację właściwą należy nałożyć płaszcz ochronny, który zabezpieczy izolację przed uszkodzeniami mechanicznymi i wpływem warunków atmosferycznych. Płaszcz powinien być montowany z zachowaniem zakładów, które zapobiegną wnikaniu wody do wnętrza izolacji.
- Konstrukcje wsporcze: W przypadku większych średnic armatury lub tam, gdzie jest to technicznie uzasadnione, należy zastosować konstrukcje wsporcze, które zapewnią stabilność izolacji i zapobiegną jej deformacji.
Przestrzeganie zasad projektowania i montażu izolacji termicznej armatury pozwala na stworzenie efektywnego systemu izolacyjnego, który minimalizuje straty ciepła, przedłuża żywotność instalacji i zapewnia optymalne warunki eksploatacyjne.
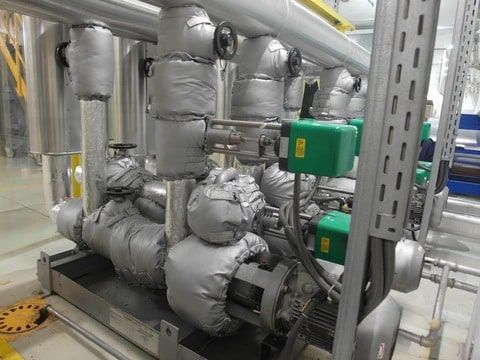
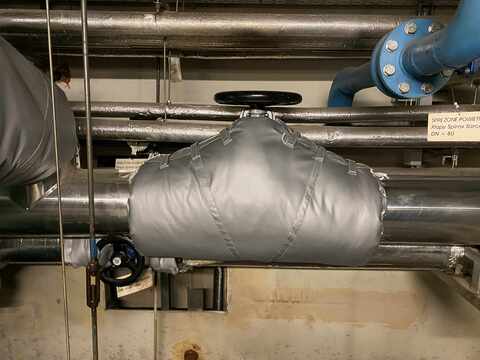
Wykonanie izolacji na armaturze
Izolacja armatury i połączeń kołnierzowych
Izolacja armatury i połączeń kołnierzowych jest kluczowym elementem w systemach grzewczych i ciepłowniczych, mającym na celu minimalizowanie strat ciepła oraz ochronę przed uszkodzeniami mechanicznymi. Właściwie wykonana izolacja zapobiega także kondensacji pary wodnej, co jest szczególnie istotne w miejscach narażonych na zmienne warunki temperaturowe.
Techniki i materiały stosowane do izolacji armatury:
- Kształtki izolacyjne: Najczęściej do izolacji armatury, takiej jak zawory, zasuwy, kolanka i połączenia kołnierzowe, stosuje się kształtki wykonane ze sztywnych porowatych materiałów izolacyjnych. Materiały te mogą obejmować wełnę mineralną, piankę poliuretanową lub inne tworzywa sztuczne charakteryzujące się niskim współczynnikiem przewodzenia ciepła.
- Wzmocnienie kształtek: Kształtki izolacyjne stosowane na armaturze często mają wzmocnioną powierzchnię zewnętrzną, np. poprzez dodanie warstwy włókna szklanego lub zastosowanie wewnętrznej wykładziny z folii aluminiowej. Takie rozwiązania zwiększają trwałość izolacji i jej odporność na uszkodzenia.
- Mocowanie kształtek: Kształtki izolacyjne są zazwyczaj mocowane za pomocą opasek wykonanych z blachy stalowej ocynkowanej lub taśm z tworzywa sztucznego. Ważne jest, aby mocowanie umożliwiało wielokrotny montaż i demontaż izolacji, co jest istotne przy konieczności serwisowania armatury.
Zasady mocowania izolacji armatury:
- Ścisłe przyleganie: Kształtki izolacyjne muszą ściśle przylegać do izolowanej powierzchni armatury, aby zapewnić pełną ochronę termiczną. Styki wzdłużne kształtek powinny być przesunięte względem siebie w przypadku wielowarstwowej izolacji, co zapobiega tworzeniu się mostków termicznych.
- Unikanie mostków cieplnych: Konstrukcje wsporcze, jeżeli są stosowane, powinny być rozmieszczone w sposób minimalizujący ryzyko powstawania punktowych mostków cieplnych, co mogłoby obniżyć skuteczność izolacji.
Specjalne wymagania mocowania izolacji armatury
Izolacja armatury wymaga uwzględnienia szczególnych elementów, które muszą być odpowiednio zabezpieczone, aby zapewnić pełną funkcjonalność systemu.
- Ochrona wrzecion: Wrzeciona zaworów i zasuw powinny być wyprowadzone na zewnątrz kształtek izolacyjnych, co umożliwia ich swobodne działanie i dostęp do nich podczas konserwacji. Powierzchnie wrzecion nie powinny być izolowane, aby zapobiec problemom z ich regulacją i ruchem.
- Demontaż połączeń: W miejscach połączeń kołnierzowych izolacja cieplna powinna być zakończona w taki sposób, aby umożliwić łatwy demontaż połączenia bez uszkodzenia izolacji. Izolacja powinna kończyć się w odległości, która pozwoli na bezproblemowy dostęp do kołnierzy.
- Silniki pomp i siłowniki zaworów regulacyjnych: Ze względu na ich specyfikę i funkcję, elementy te nie są zazwyczaj izolowane. Ważne jest, aby te komponenty miały swobodny dostęp do powietrza, co zapobiega ich przegrzewaniu się.
Prawidłowe wykonanie izolacji armatury, z uwzględnieniem specyficznych wymagań poszczególnych elementów, jest kluczowe dla zapewnienia efektywności energetycznej całej instalacji oraz jej długotrwałej bezawaryjnej pracy. Odpowiednio dobrane i zamontowane materiały izolacyjne skutecznie chronią przed stratami ciepła, a także zwiększają trwałość i bezpieczeństwo systemów grzewczych i ciepłowniczych.
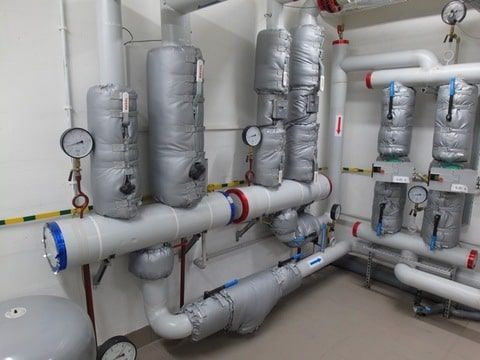
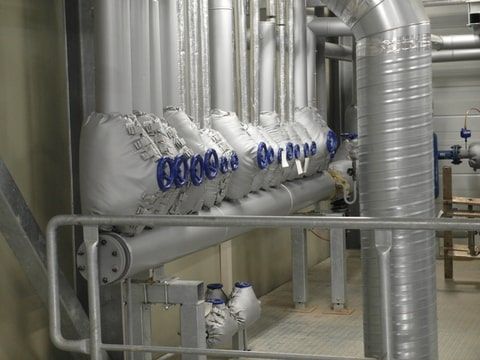
Techniki montażu płaszczy ochronnych armatury
Prawidłowy montaż płaszczy ochronnych jest kluczowy dla zapewnienia trwałości i skuteczności izolacji termicznej armatury. Niewłaściwie zamontowany płaszcz może prowadzić do wnikania wody, co z czasem uszkodzi izolację i obniży jej właściwości izolacyjne.
Zasady prawidłowego montażu płaszczy ochronnych:
- Zachowanie zakładów: Przy montażu płaszczy ochronnych kluczowe jest zachowanie odpowiednich zakładów na stykach wzdłużnych i poprzecznych elementów. Zakłady te powinny być na tyle duże, aby zapewnić pełne pokrycie izolacji i uniemożliwić wnikanie wody. Zaleca się, aby zakłady wynosiły co najmniej 50 mm, co daje pewność, że płaszcz ochronny spełni swoją funkcję.
- Łączenie elementów: Płaszcze ochronne, zwłaszcza te wykonane z blachy stalowej ocynkowanej lub taśm aluminiowych, powinny być łączone za pomocą wkrętów, nitów lub taśm zabezpieczonych przed korozją. Miejsca łączeń powinny być starannie zabezpieczone, aby uniknąć powstawania nieszczelności, które mogłyby prowadzić do wnikania wody lub powietrza.
- Zabezpieczenie przed wnikaniem wody: W przypadku instalacji narażonych na działanie warunków atmosferycznych, szczególną uwagę należy zwrócić na uszczelnienie zakładów i połączeń elementów płaszcza. Można zastosować specjalne taśmy uszczelniające lub pasty bitumiczne, które dodatkowo zabezpieczą przed wnikaniem wody. W instalacjach znajdujących się w podziemnych kanałach czy w miejscach o wysokiej wilgotności płaszcz ochronny może być wyposażony w opaski lub przekładki wentylacyjne, które umożliwiają odprowadzenie wilgoci i wentylację izolacji.
- Dostosowanie do warunków eksploatacyjnych: Płaszcze ochronne powinny być montowane z uwzględnieniem warunków, w jakich będzie pracować instalacja. W miejscach o dużym natężeniu ruchu lub tam, gdzie izolacja może być narażona na uszkodzenia mechaniczne, stosuje się dodatkowe wzmocnienia płaszcza lub używa się bardziej odpornych materiałów, takich jak grubsze blachy stalowe.
Prawidłowy montaż płaszczy ochronnych jest nieodzowny dla zapewnienia długotrwałej ochrony izolacji armatury. Właściwie dobrany i zamontowany płaszcz ochronny nie tylko zabezpiecza izolację przed uszkodzeniami, ale także przedłuża jej żywotność, co ma bezpośredni wpływ na efektywność energetyczną całego systemu grzewczego czy ciepłowniczego.
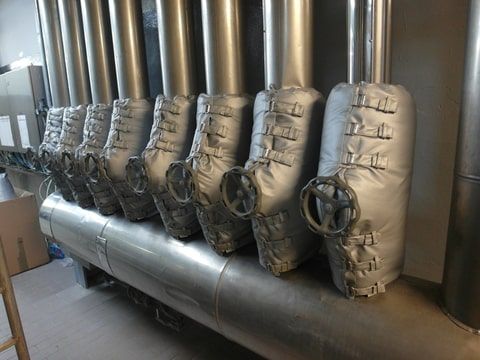
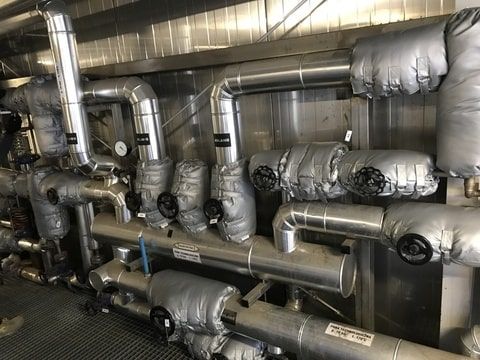
Kontrola jakości i odbiory izolacji armatury
Odbiór materiałów izolacyjnych
Odbiór materiałów izolacyjnych jest pierwszym i niezwykle ważnym etapem kontroli jakości w procesie izolacji armatury. Prawidłowo przeprowadzony odbiór materiałów zapewnia, że użyte produkty spełniają wszystkie wymagane normy i będą odpowiednio pełnić swoją funkcję izolacyjną.
Procedury odbioru materiałów izolacyjnych armatury:
- Sprawdzenie dokumentacji: Pierwszym krokiem jest weryfikacja dokumentacji dostarczonej przez producenta materiałów izolacyjnych. Każda partia materiałów powinna być opatrzona etykietą lub dokumentem identyfikacyjnym, który zawiera takie informacje jak: nazwa producenta, typ i rodzaj materiału, numer partii, data produkcji oraz znak kontroli jakości. Ponadto, materiały powinny być dostarczone wraz z certyfikatem zgodności z odpowiednimi normami, takimi jak PN-B-02421, co gwarantuje ich zgodność z wymaganiami technicznymi.
- Inspekcja wizualna: Po weryfikacji dokumentacji, należy przeprowadzić inspekcję wizualną materiałów. W ramach tego etapu ocenia się stan powierzchni materiałów, zwracając uwagę na wszelkie uszkodzenia, takie jak pęknięcia, zagniecenia, czy nierówności, które mogłyby wpłynąć na jakość izolacji. Powierzchnie oraz krawędzie materiałów powinny być gładkie, równe i wolne od uszkodzeń.
- Weryfikacja wymiarów: Materiały izolacyjne powinny mieć wymiary zgodne z zamówieniem i wymaganiami norm. Ewentualne odchyły wymiarów powinny mieścić się w granicach dopuszczonych przez normy techniczne. Ważne jest również, aby sprawdzić, czy materiały są odpowiednio opakowane, co zabezpiecza je przed uszkodzeniami mechanicznymi i zawilgoceniem podczas transportu i składowania.
- Sprawdzenie zgodności z normami: Ostatecznym krokiem jest potwierdzenie, że materiały izolacyjne posiadają wymagane certyfikaty jakości oraz spełniają specyficzne normy dotyczące bezpieczeństwa pożarowego, higieny oraz ochrony środowiska, które są niezbędne w zależności od miejsca montażu izolacji.
Odbiory izolacji armatury
Odbiór wykonanej izolacji to kluczowy etap w procesie izolacji armatury, który zapewnia, że izolacja została zainstalowana zgodnie z wymaganiami technicznymi i spełnia wszystkie niezbędne normy jakościowe. Odbiór końcowy izolacji obejmuje dokładne sprawdzenie grubości, jakości wykonania oraz montażu płaszcza ochronnego.
Procedury odbioru końcowego izolacji armatury:
- Sprawdzenie grubości izolacji: Grubość wykonanej izolacji powinna być zgodna z dokumentacją techniczną oraz normami, takimi jak PN-B-02421. Pomiar grubości izolacji przeprowadza się w kilku losowo wybranych miejscach, w tym na początku, w środku i na końcu izolowanego odcinka armatury. W przypadku izolacji wykonanej z miękkich materiałów, takich jak wełna mineralna, pomiary wykonuje się w dwóch kierunkach – w pionie i w poziomie. Dopuszczalne odchyłki grubości wynoszą zazwyczaj od -5% do +10% względem założonej grubości.
- Ocena jakości wykonania: Kolejnym etapem jest ocena jakości wykonania izolacji. Należy sprawdzić, czy izolacja jest równomiernie ułożona na całej powierzchni armatury, bez widocznych zwisów, zapadnięć czy innych nierówności, które mogłyby wpłynąć na jej efektywność. Ważne jest także, aby styki wzdłużne i poprzeczne elementów izolacji były odpowiednio doszczelnione, co zapobiega tworzeniu się mostków termicznych.
- Kontrola montażu płaszcza ochronnego: Ostatnim etapem odbioru końcowego jest kontrola montażu płaszcza ochronnego. Płaszcz powinien być równomiernie ułożony na całej powierzchni izolacji, bez pęknięć, wgnieceń i innych uszkodzeń mechanicznych. Należy również upewnić się, że wszystkie połączenia, zarówno wzdłużne, jak i poprzeczne, są odpowiednio zabezpieczone przed wnikaniem wody. W przypadku instalacji zewnętrznych lub narażonych na wilgoć, szczególną uwagę należy zwrócić na szczelność płaszcza oraz zastosowanie odpowiednich uszczelnień i systemów wentylacyjnych.
- Sprawdzenie konstrukcji wsporczych: Jeżeli w izolacji zastosowano konstrukcje wsporcze, powinny one być sprawdzone pod kątem prawidłowego rozmieszczenia i stabilności. Konstrukcje te powinny zapewniać, że izolacja nie będzie narażona na deformacje podczas eksploatacji.
Zakończenie odbioru końcowego powinno być potwierdzone protokołem odbioru, który dokumentuje, że izolacja armatury została wykonana zgodnie z wymaganiami technicznymi i spełnia wszystkie kryteria jakościowe. Tylko takie podejście gwarantuje, że izolacja będzie efektywnie spełniać swoją funkcję przez długi czas, przyczyniając się do obniżenia strat ciepła i poprawy efektywności energetycznej całej instalacji.
Korzyści z prawidłowej izolacji armatury
- Oszczędność energii i redukcja kosztów:
Prawidłowa izolacja armatury, zgodnie z wymaganiami określonymi w normie PN-B-02421:2000, odgrywa kluczową rolę w minimalizowaniu strat ciepła w systemach grzewczych i ciepłowniczych. Izolacja armatury ogranicza niekontrolowane wycieki energii, co bezpośrednio przekłada się na zmniejszenie zużycia paliwa lub energii potrzebnej do podgrzewania wody i innych mediów. Dzięki temu obniżają się koszty eksploatacyjne systemu. Co więcej, efektywne zarządzanie stratami ciepła pozwala na lepsze wykorzystanie zainstalowanych systemów, co może prowadzić do zmniejszenia zapotrzebowania na dodatkowe źródła ciepła. - Zwiększenie trwałości i bezpieczeństwa instalacji:
Izolacja armatury nie tylko wpływa na oszczędność energii, ale również na długowieczność i niezawodność całej instalacji. Poprzez ograniczenie strat ciepła, izolacja chroni armaturę przed skrajnymi temperaturami, które mogą powodować deformacje, pęknięcia lub inne uszkodzenia mechaniczne. Ponadto, prawidłowo zaizolowane elementy są mniej narażone na kondensację, co zmniejsza ryzyko korozji i wydłuża żywotność systemów. W konsekwencji izolacja armatury przyczynia się do poprawy bezpieczeństwa całej instalacji, zmniejszając ryzyko awarii, które mogłyby prowadzić do kosztownych napraw lub przerw w dostawie ciepła.
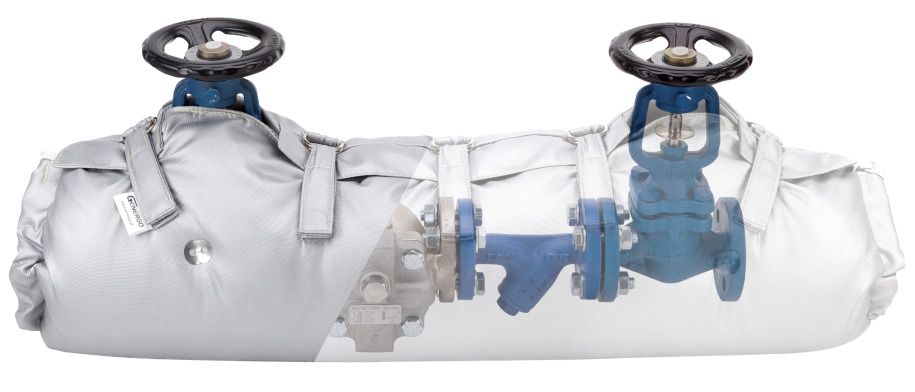
Izolacja armatury - pokrowce termoizolacyjne
Pokrowce termoizolacyjne do armatury takiej jak THERMO-GEN STANDARD™ oferowane przez Genergo są praktycznym rozwiązaniem zgodnym z wymaganiami norm, przeznaczonym do ochrony armatury przed stratami ciepła i uszkodzeniami mechanicznymi, wspierając tym samym oszczędność energii i bezpieczeństwo instalacji.
Pokrowce termoizolacyjne odgrywają kluczową rolę w zapewnieniu efektywności energetycznej oraz ochronie elementów systemów grzewczych i ciepłowniczych. W szczególności, produkty THERMO-GEN STANDARD™ oferowane przez firmę Genergo stanowią nowoczesne rozwiązanie przeznaczone do izolacji armatury przemysłowej.
Pokrowce termoizolacyjne do armatury od Genergo są specjalnie zaprojektowane, aby minimalizować straty ciepła, co bezpośrednio przekłada się na obniżenie kosztów eksploatacyjnych oraz zwiększenie efektywności energetycznej. Są wykonane z materiałów o wysokiej odporności na warunki zewnętrzne, co zapewnia długą żywotność i niezawodność.
Dzięki ich konstrukcji możliwe jest ich łatwe montowanie i demontowanie, co jest szczególnie istotne podczas prac konserwacyjnych.
Uniwersalne pokrowce do izolacji armatury
Uniwersalność pokrowców THERMO-GEN STANDARD™ sprawia, że są kompatybilne z urządzeniami różnych producentów, co czyni je wszechstronnym rozwiązaniem dla wielu rodzajów instalacji.
Dodatkową zaletą jest natychmiastowa dostępność pokrowców w standardowych rozmiarach, co pozwala na szybkie wdrożenie izolacji w nowych lub modernizowanych systemach. Pokrowce THERMO-GEN STANDARD™ nie tylko spełniają wymagania norm, ale także przewyższają tradycyjne metody izolacji pod względem łatwości użycia, co czyni je idealnym wyborem dla inwestorów i wykonawców dążących do optymalizacji energetycznej swoich instalacji.
Podsumowując, pokrowce termoizolacyjne THERMO-GEN STANDARD™ to praktyczne i skuteczne rozwiązanie, które nie tylko zabezpiecza armaturę przed stratami ciepła, ale również zwiększa trwałość i niezawodność całego systemu, zgodnie z najwyższymi standardami technicznymi.
Izolacja armatury - podsumowanie
Izolacja armatury jest nieodzownym elementem efektywnych systemów grzewczych i ciepłowniczych. Kluczowe aspekty, które należy uwzględnić, to odpowiedni dobór materiałów izolacyjnych, ich grubość oraz właściwe wykonanie izolacji zgodnie z normą PN-B-02421:2000. Ważne jest również uwzględnienie czynników, takich jak ochrona przed wilgocią i uszkodzeniami mechanicznymi, które mogą wpływać na trwałość izolacji. Prawidłowo wykonana izolacja armatury nie tylko zmniejsza straty ciepła, ale również zapewnia długotrwałą i bezawaryjną pracę systemu, chroniąc jego elementy przed uszkodzeniami.
Izolacja armatury - Rekomendacje dla inwestorów i wykonawców
Inwestorzy i wykonawcy powinni zwrócić szczególną uwagę na przestrzeganie wymagań określonych w normie oraz stosowanie materiałów o potwierdzonej jakości i zgodności z odpowiednimi standardami. Przed przystąpieniem do prac izolacyjnych należy upewnić się, że wszystkie powierzchnie są odpowiednio przygotowane, suche i zabezpieczone przed korozją. Izolację armatury najlepiej wykonywać w sprzyjających warunkach atmosferycznych, unikając pracy podczas opadów, co minimalizuje ryzyko zawilgocenia materiałów. Regularne kontrole i odbiory międzyoperacyjne zapewnią, że izolacja została wykonana zgodnie z projektem, co przyczyni się do optymalnej efektywności energetycznej oraz zwiększenia żywotności instalacji.