Thermal insulation installation in industrial facilities
Installation of thermal insulation in industrial facilities is of paramount importance for efficiency and safety. In the article, we discuss the crucial significance of thermal insulation installation in industrial facilities to achieve optimal performance and safety.
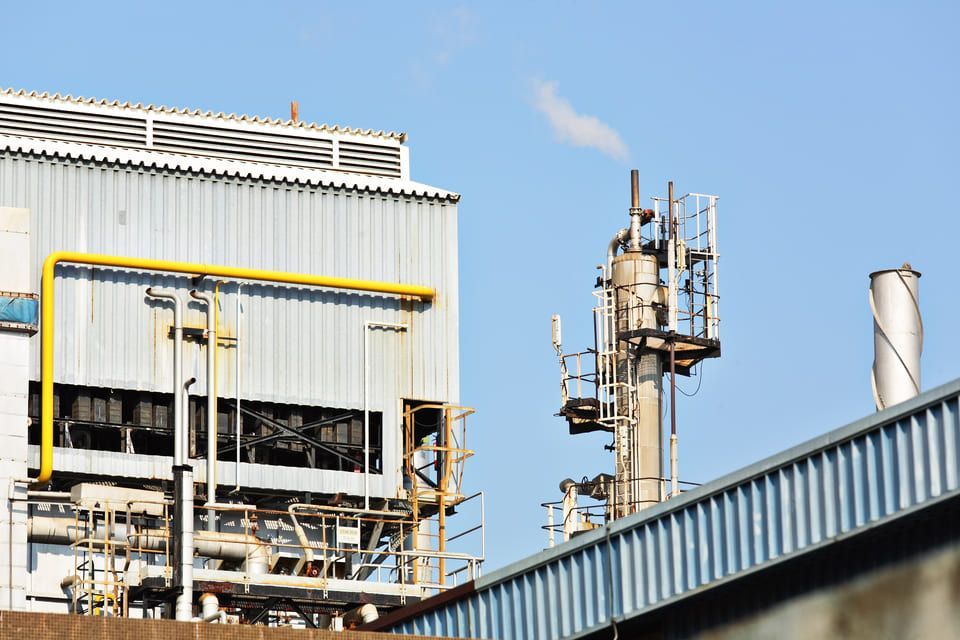
Proper installation of thermal insulation in industrial facilities is crucial for maintaining efficiency and safety. Thermal insulation plays a significant role in limiting heat exchange and preventing energy losses, ensuring optimal functioning of equipment and processes. In this article, we will discuss the importance of thermal insulation installation in industrial facilities and provide valuable insights into best practices and considerations for correct thermal insulation installation.
Why is thermal insulation installation important in industrial facilities?
Industrial facilities in factories, power plants, and refineries generate heat. Without proper thermal insulation, heat can escape from systems, leading to energy wastage and inefficiency.
Thermal insulation installation in industrial facilities is essential for several reasons:
- Energy efficiency: Properly installed thermal insulation reduces heat transfer, helping to maintain desired temperature levels in industrial equipment and systems. This results in improved energy efficiency and reduced energy consumption.
- Process optimization: Industrial processes often require precise temperature control. Insulation prevents heat loss, ensuring consistent maintenance of desired temperatures. Such optimization enhances overall industrial facility performance and productivity.
- Equipment protection: Thermal insulation acts as a protective barrier, shielding equipment and pipelines from extreme temperatures. It helps prevent thermal stress, corrosion, and damage, thereby extending the equipment's lifespan.
- Personnel safety: By minimizing heat radiation and equipment temperatures, thermal insulation installation in industrial facilities reduces the risk of burns and injuries to personnel working near hot equipment or pipelines.
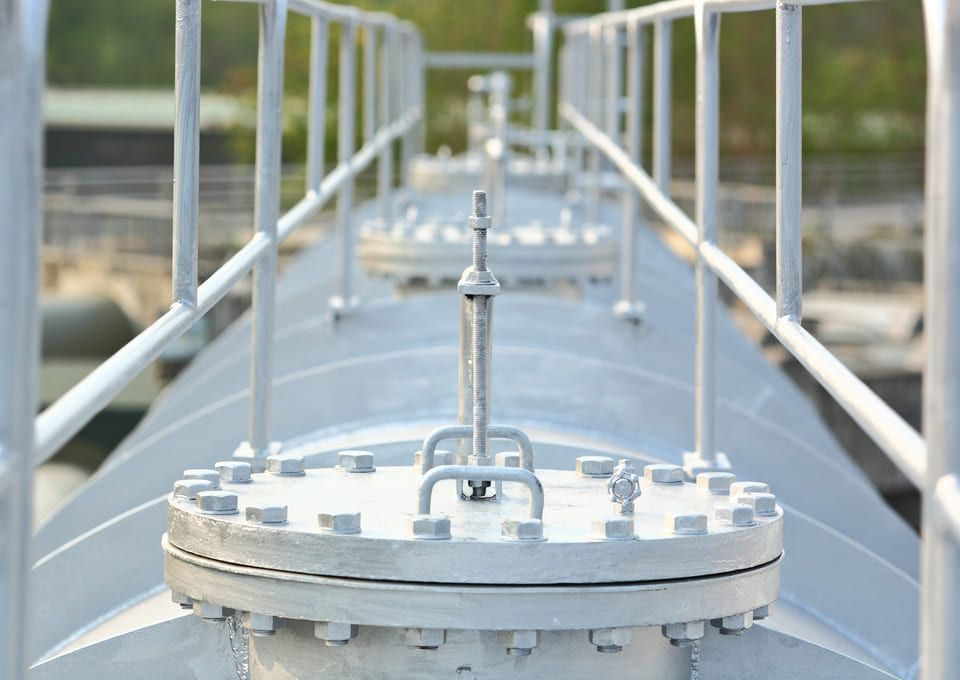
Best practices for thermal insulation installation in industrial facilities:
Before commencing insulation installation, comprehensive inspection and assessment of the industrial facility are crucial. This assessment should include:
- Identification of areas requiring insulation: Determining specific equipment, pipelines, and systems that require thermal insulation based on their temperature profiles and heat loss potential.
- Measurements and calculations: Accurately measuring the surface dimensions to be insulated and calculating the required insulation thickness to achieve desired temperature control.
- Surface preparation: Ensuring that surfaces designated for insulation are clean, dry, and free from any contaminants that may hinder the adherence of the insulation material.
Selection of the appropriate insulation material
Choosing the right insulation material is critical for the effectiveness and durability of the thermal insulation system. When selecting insulation material, consider the following factors:
- Thermal conductivity: Opt for materials with low thermal conductivity to minimize heat transfer.
- Temperature range: Ensure that the insulation material is suitable for the temperature range of the industrial installation.
- Environmental factors: Take into account the presence of moisture, chemicals, or other corrosive substances in the environment and select materials capable of withstanding such conditions.
Compliance with safety regulations and standards
During thermal insulation installation in industrial facilities, adherence to safety regulations and industry standards is paramount. This includes:
- Fire safety compliance: Choose insulation materials with appropriate fire resistance ratings and ensure they are installed in accordance with fire safety regulations.
- Personal protective equipment: Provide adequate personal protective equipment, such as gloves, goggles, and respiratory protection, to workers involved in insulation installation to safeguard their health.
- Regulatory compliance: Familiarize with relevant regulations and standards concerning thermal insulation in industrial facilities, as established by safety and occupational health authorities.
Regular maintenance and inspection
After completing the thermal insulation installation, implementing a regular maintenance and inspection program is necessary. This program should include:
- Visual inspections: Periodically inspect the insulation system for signs of damage, degradation, or moisture ingress. Address any issues promptly to maintain insulation effectiveness.
- Repair and replacement: If any insulation material or system component is damaged, worn out, or no longer effective, replace or repair it to ensure continuous thermal insulation.
By following these best practices, industrial facilities can benefit from improved energy efficiency, process optimization, equipment protection, and personnel safety.
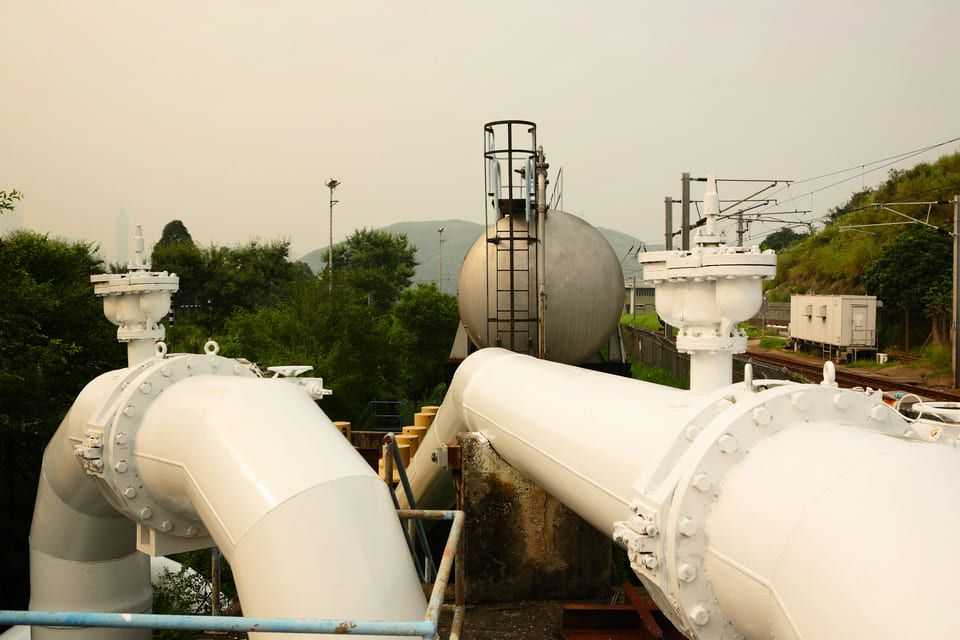
Frequently asked questions (FAQ)
What are the typical applications of thermal insulation in industrial facilities?
Thermal insulation is used in various industrial sectors, including energy, oil and gas, chemical processing, HVAC systems, and manufacturing. It serves to insulate equipment, pipelines, storage tanks, boilers, furnaces, and other elements that generate or transport heat.
How can thermal insulation contribute to cost savings in industrial facilities?
Thermal insulation helps reduce energy consumption by minimizing heat losses. By saving energy, industrial facilities can achieve significant cost savings in heating or cooling expenses, leading to improved operational efficiency and lower utility bills.
Are there any environmental benefits associated with thermal insulation installation in industrial facilities?
Yes, proper thermal insulation in industrial facilities contributes to environmental sustainability. By reducing energy consumption, it helps lower greenhouse gas emissions, decrease dependence on fossil fuels, and mitigate the carbon footprint associated with industrial processes.
How long does thermal insulation last in industrial facilities?
The lifespan of thermal insulation in industrial facilities depends on various factors, including the type of insulation material, environmental conditions, maintenance practices, and exposure to physical or chemical loads. Well-maintained and correctly installed insulation systems can last for several decades.